
Nichrome, a widely used nickel-chromium alloy, is best known for its excellent heat and oxidation resistance. Due to its ability to maintain mechanical integrity at high temperatures, it’s a top choice for heating elements and industrial furnaces. This blog will explore the alloy’s composition, performance characteristics, use cases, grade designations, and innovation landscape through PatSnap Eureka AI Agent.
What is Nichrome?
It is a non-magnetic alloy composed mainly of nickel (Ni) and chromium (Cr), with possible additions of iron or other elements. The most common formulation, Nichrome 80/20, contains 80% nickel and 20% chromium. This alloy forms a stable oxide layer at high temperatures, protecting it from corrosion and oxidation.
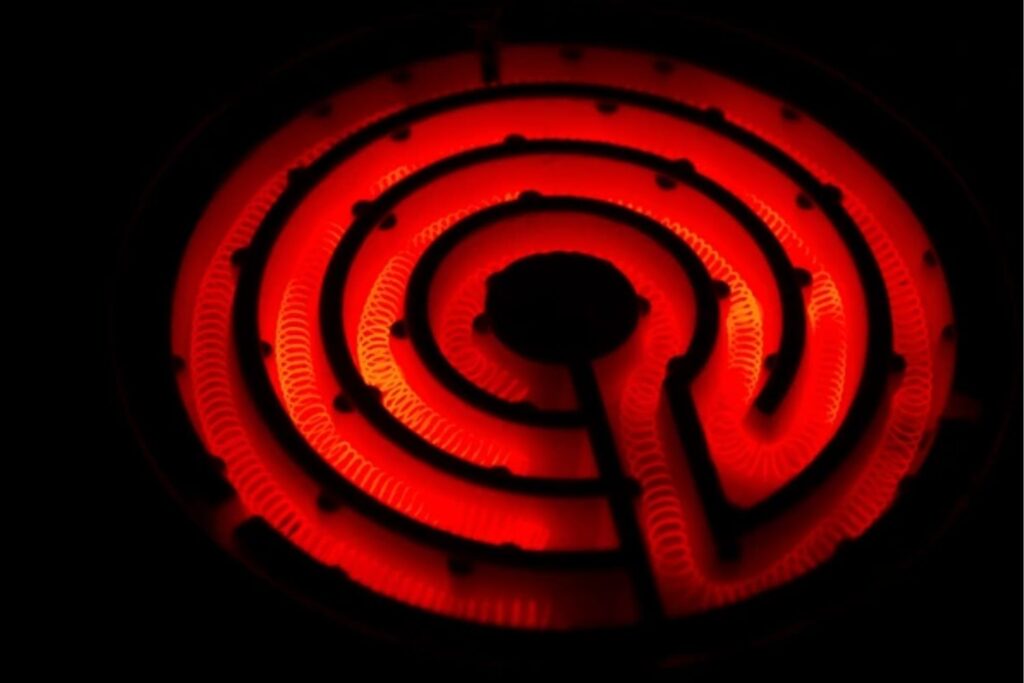
Composition & Properties / Performance
Chemical Composition
- Common Formula: NiCr (80% nickel / 20% chromium)
- CAS Number: 12605-21-7 (Nichrome)
- Other Elements (optional): Fe, Si, Mn
Physical & Mechanical Properties
- Density: ~8.4 g/cm³
- Melting Point: ~1400–1450°C
- Electrical Resistivity: ~1.10–1.50 Ω⋅mm²/m
- Tensile Strength: ~600–900 MPa
- Maximum Operating Temperature: ~1200°C
Functional Properties
- High electrical resistance
- Excellent oxidation resistance
- Maintains shape and strength at high temperatures
- Non-magnetic and corrosion resistant
Material Grades & Designations
Common Grades
- Nichrome 80/20: High resistivity, ideal for heating elements
- Nichrome 60/15: Lower resistivity, higher flexibility
- Nichrome 35/20: With added iron, better mechanical strength
Cross-Reference Table
Grade | Ni % | Cr % | Features |
---|---|---|---|
Nichrome 80/20 | 80 | 20 | High resistivity, long life |
Nichrome 60/15 | 60 | 15 | More ductile, easier to fabricate |
Nichrome 35/20 | 35 | 20 | Tougher, better for mechanical loads |
Application Landscape
Key Industries
- Electronics: Heating elements in toasters, hair dryers, soldering irons
- Industrial: Kilns, heat sealing machines, furnaces
- Aerospace: Anti-icing systems, resistive heating for fluid systems
- Medical: Dental tools, cauterization devices
Real-World Examples
- Nichrome wire in e-cigarettes and vaping devices
- Resistance heating coils in laboratory equipment
- High-temperature heating bands in plastic extrusion machinery
Emerging Trends
- Miniaturized nichrome circuits in flexible electronics
- Additive manufacturing of nichrome-based thermal components
- Thin nichrome films in wearable thermotherapy devices
Nichrome vs Other Similar Materials
Property | Nichrome | Kanthal | Copper |
---|---|---|---|
Max Temp (°C) | ~1200 | ~1400 | ~105 |
Oxidation Resistance | Excellent | Excellent | Poor |
Electrical Resistivity | High | Moderate | Very Low |
Mechanical Strength | Moderate | High | Low |
Advantages of Nichrome
- High Temperature Resistance: Performs reliably at up to 1200°C, maintaining shape and resistive efficiency.
- Excellent Oxidation Resistance: Forms a stable Cr2O3 layer that protects against degradation in open-air heating environments.
- Long Lifespan: Capable of handling repeated heating and cooling cycles without significant performance loss.
- Uniform Heating: Its consistent electrical resistivity ensures smooth, even heat distribution across coils and filaments.
- Formability: Nichrome wires and ribbons can be easily bent, wound, or patterned for various heating geometries.
- Low Thermal Expansion: It expands minimally under heat, helping retain structural dimensions in high-precision applications.
- Non-Magnetic: Ideal for use in electronic systems where magnetism could cause interference.
- Corrosion Resistance: Resists oxidation, sulfur attack, and scaling in most oxidizing atmospheres.
- Stable Performance: Works efficiently across a broad range of voltages and currents.
Innovations & Technology
Recent Developments
- 3D-Printed Nichrome Components: Additive manufacturing enables production of custom heating elements for aerospace, automotive, and biomedical industries. This reduces waste and allows complex geometries.
- Flexible Nichrome Heaters: Nichrome films printed onto flexible substrates are powering wearable thermotherapy systems and textile-integrated heating.
- Microfabricated Nichrome Structures: Used in microelectromechanical systems (MEMS) for precise, localized heating in analytical devices.
- Multi-Layer Nichrome Films: Employed in printed circuit boards (PCBs) and thermal interface materials for advanced thermal control.
- Protective Coatings: Surface treatments extend durability in harsh environments, such as acidic or high-moisture industrial settings.
- Low-Voltage Nichrome Alloys: New formulations optimized for battery-operated and portable electronic devices.
- Thermal Imaging Integration: Research explores embedding nichrome grids within IR-transparent films for self-regulating surfaces.
Sustainability & Environmental Impact
- Recyclability: Fully recyclable and often reused in alloy recovery systems.
- Low Environmental Hazard: Stable during use; minimal leaching or emissions.
- Energy Efficiency: Converts electricity to heat with high reliability.
- Compliance: Can meet RoHS and REACH standards when properly formulated.
Conclusion
Nichrome remains indispensable in industries requiring high-temperature, reliable resistive heating. Its unique combination of strength, corrosion resistance, and electrical properties supports a wide range of applications from consumer electronics to aerospace. With innovations like 3D-printed heating elements, MEMS integration, and smart textile applications, it is poised to evolve alongside future thermal technologies.
FAQs
No. Nichrome is a non-magnetic alloy, ideal for electronic and heating applications.
It is primarily used in heating elements like toaster wires, furnaces, and e-cigarettes.
Not with standard solder; it often requires spot welding or crimping due to its oxide layer.
Typically between 1400–1450°C, depending on grade composition.
It is highly corrosion-resistant due to a protective chromium oxide layer.
For more scientific explanations of nichrome , try PatSnap Eureka AI Agent.
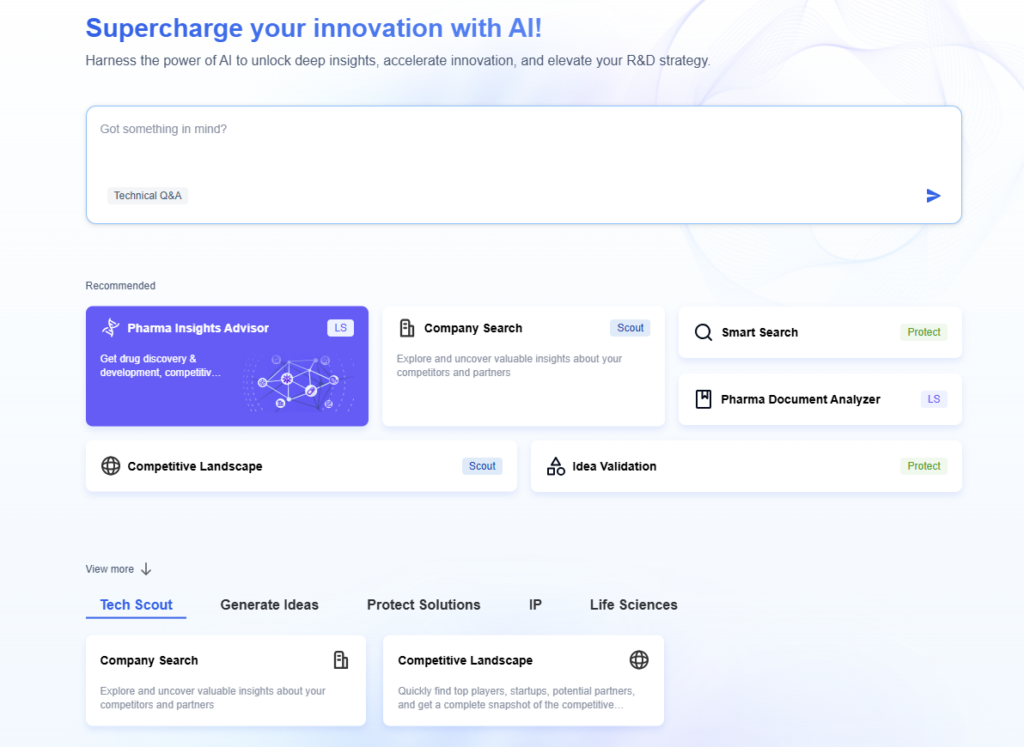
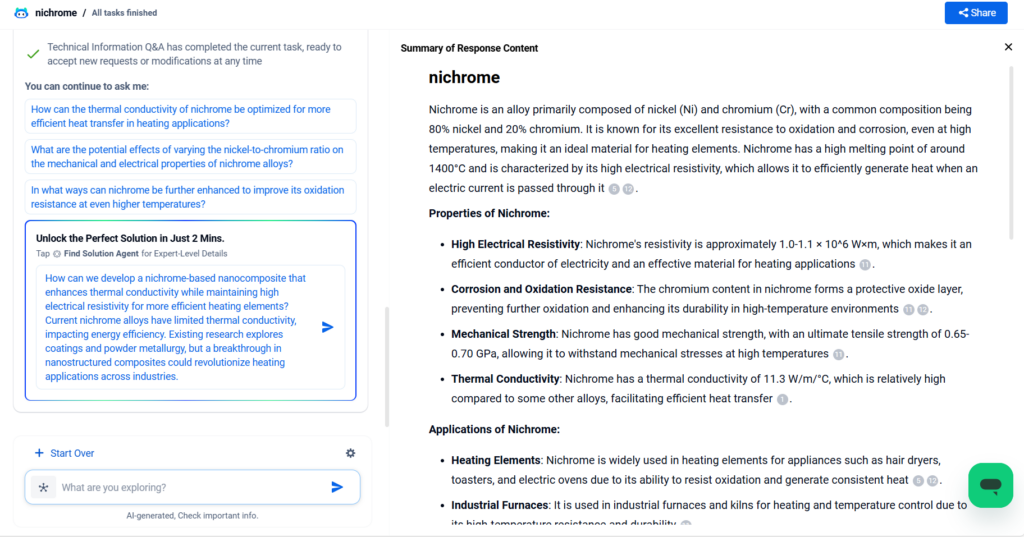
